Predictive Maintenance Grounded on the Internet of Things February 15, 2022
The industrial Internet of things (IoT) uses smart sensors and actuators to improve manufacturing and industrial processes. Also known as Industry 4.0, the Internet of things uses intelligent machines and real-time data to communicate important information. For example, smart sensors can immediately pick up on inefficiencies and red flags, saving time, money, and other resources for the organization.
What Does the Internet of Things (IoT) Have to Do With Predictive Maintenance?
Predictive maintenance (PdM) is the servicing of equipment when optimally warranted. Predictive maintenance uses proactive methods to analyze equipment conditions and estimate when maintenance should be performed to save time and money.
Internet of things (IoT) devices used in the manufacturing industry enable predictive maintenance by helping to predict when a machine should be serviced. In this way, the necessary maintenance can be performed before a catastrophic failure occurs. And an organization can better achieve operational efficiency.
Components of IoT-Based Predictive Maintenance
Specific components carry out Internet of things-based predictive maintenance:
- Sensors: collect all the machine data by installing them at particular points
- Data communication: a system that permits data from sensors to move to a centralized data storage
- Central data storage: where all the machine data and business data coming from other IT systems is housed
- Predictive maintenance software: streams all data to maintenance teams and lets them know when the machine is operating beyond its specified range
- Predictive analytics: includes analytics programs that are applied to the data to generate actionable insights
Benefits Of the Internet of Things (IoT)
According to the Predictive Maintenance Report by PWC, predictive maintenance in manufacturing can reduce costs by 12%, improve uptime by 9%, extend asset life by 20%, and reduce safety hazards and risks by 14%.
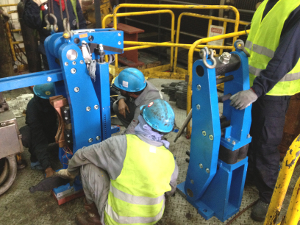
Reduce Maintenance Costs
One of the primary benefits of IoT devices in the manufacturing industry is reducing maintenance costs. By proactively addressing maintenance issues, an organization can better achieve operational efficiency by using real-time data to predict when a machine needs service.
Extend Asset Life
Extended asset life is another benefit of IoT technologies. IoT-based predictive maintenance allows you to monitor, maintain, and optimize assets for better availability and performance. You can accurately identify components that need replacement schedule replacement, and repairs on time, extending the life of your machines.
Improve Asset Reliability
IoT-based predictive maintenance promotes more efficient use of current assets by predicting machine failures and decreasing maintenance issues. Determining the cause of delays and setting up processes to address these causes leads to improved asset reliability.
Improve Safety & Compliance
IoT-based predictive maintenance allows you to monitor operational conditions and flag hazards or risks posed to workers if left unresolved. You can analyze internal and external data sources with the data from IoT devices and quickly take appropriate action.
To implement an IoT-based predictive maintenance strategy, you will need to determine which assets need predictive maintenance. If your plant is in Ontario, Duke conducts free critical motor assessments. We are equipped to conduct assessments over phone/video chats if you're outside of Ontario.
Get Your FREE Critical Motor Assessment