Noise and Vibration Analysis of Electric Motors February 15, 2022
Noise and vibrations generated by an electric motor can be divided into three main contributors: mechanical, aerodynamic, and electromagnetic.
Mechanical Noise and Vibration
Mechanical noise and vibration are related to manufacturing or mechanical conditions like friction, alignment or lubrication faults, and loss of contact between bearings, gears, and other interfaces. These conditions are dependent on rotational speed, load, and temperature.
There are several transfer paths for noise and vibration generated by an electric motor:
- Airborne noise radiated by the motor frame or any structural part of the motor. The vibration is transmitted through the support structure and converted to airborne sound waves at the resounding component.
- Structure-borne noise is transmitted to the structure by the stator through its mountings. The transmitted vibration waves cause noise and can also be hazardous to the structure.
- Noise due to excitation of gearboxes and couplings, caused by torque ripple. Torque ripple is a periodic disturbance in torque, with a frequency and an amplitude component (an AC imposed over DC value, driven by excitation and construction).
Mitigation strategies for mechanical noise include, but are not limited to:
- Modification of damaged ball bearings
- Use of chemical additives
- Use of vibration absorption or vibration isolation device
- Modification of rotating speed
- Use of alignment tools when mounting the motor
- Application of shield or seal to prevent dirt from entering the bearings
- Dynamic rotor balancing
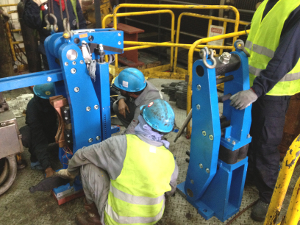
Aerodynamic Noise and Vibration
Aerodynamic noise most often occurs around the ventilation system or in the area of the machine that behaves like a fan. This noise is prevalent at higher motors speeds and in electric vehicles due to higher speed fluctuation. Characteristic frequencies of aerodynamic noise in electric machines include vortex frequency, blade passing frequency, and rotor duct passing frequency.
Electromagnetic Noise and Vibration
Electromagnetic noise and vibrations are the primary type of noise and vibrations for the widely used small and medium-sized electrical machines. The noise comes from the vibrations of the electric motor in the audible range under the excitation of electromagnetic forces, including magnetostriction and Maxwell forces.
Magnetostriction in noise generation can generally be ignored, as it is not usually the cause of electromagnetic noise and vibrations in rotating machines.
Maxwell stress is the formalization of how magnetic forces arise from electromagnetic fields. It includes attraction and repulsion forces between two magnets, reluctant forces which can shorten the magnetic field lines, and Laplace forces that apply on electric currents in external magnetic fields.
To mitigate or manage electromagnetic noise:
- Avoid resonance between magnetic forces and structural modes
- Reduce asymmetries, so tolerance is on
- Eccentricities
- Magnet position/magnetization
- Lamination roundness
Importance of Noise and Vibration Analysis
Sound and vibration analysis can help manufacturers prevent hazardous sound and vibration levels and evaluate the cause of product or system failures. Certified specialists can take sound measurements or place an accelerometer on an item to obtain accurate results. Sound and vibration are dependent on test conditions like temperature, ambient noise, and whether the inputs are coming from the right excitation source.
Why Your Maintenance Program Needs Vibration Analysis
- It saves money.Vibration analysis is a way to identify potential issues with the equipment before they become a problem, reducing downtime and repair costs and increasing equipment life, safety and production.
- It’s quantitative. Vibration analysis is all about the numbers. It uses sophisticated tools and software to generate data, which engineers and analysts can use to take action.
- It can be continuous. Tools and software can be installed on equipment to monitor vibrations in real-time 24/7. Readings can be sent to your computer, tablet or phone.
- It’s non-invasive. Vibration analysis can be conducted while your equipment operates, so there’s no need for lost production time.
- It can be used to establish equipment baselines. Vibration analysis is an excellent way to establish acceptance testing criteria so you can evaluate whether equipment installation and repairs are done right.
- It’s perfect for particular types of equipment. No one wants to shut down critical production or go into hostile environments more than they have to. Essential, heavily used, and difficult-to-access equipment are all excellent choices for vibration analysis, mainly if it’s done continuously.